Just Because a Supplier Wants to Recycle its Waste Doesn't mean it Can
By Kim van der Weerd, August 30, 2023
Reflections from August’s Supplier Meet-Up
Supplier Meet-Ups are private, off-the-record conversations open only to suppliers, held once per month, and hosted by the Asia Garment Hub. Each month, one supplier shares a specific challenge they’re facing while the rest of the group shares feedback and offers support. We’re a small group interested in developing meaningful interpersonal relationships. More often than not, the challenges raised during these sessions are shared, and, occasionally, they serve as a catalyst for more formal collaborations.
For example, a number of regular Supplier Meet-Up participants were key supporters of the recently released resource An Apparel Supplier’s Guide: Key Sustainability Legislations in the EU, US, and UK commissioned by Epic Group, Simple Approach, Shahi Exports, Norlanka and supported by the Asia Garment Hub and Transformers Foundation. Other suppliers have joined forces to co-commission a forthcoming white paper about the difficulty suppliers face in financing decarbonization.
Like the legislative landscape and the difficulty of financing decarbonization, the challenge presented at August’s meet-up – waste management – resonated broadly across the group. The supplier in question currently has a contract with a private waste management company to incinerate its textile waste. They want to recycle their fabric waste but are facing a number of infrastructural, legal, political, and economic barriers.
For example, recycling infrastructure in their country is virtually non-existent. Furthermore, the country’s waste management services are monopolized by a small group of companies with close ties to the government – and have a vested interest in the status quo. The supplier noted that, as a result, there is little political appetite for developing recycling infrastructure.
Legally, the supplier also faces barriers to recycling its textile waste. They have a license from the government to import fabrics duty-free (because fabrics are not produced locally). These licenses are designed to attract foreign investment into the country. Maintaining the license requires being able to prove that all imported textile has been exported as a finished product.
This has two practical consequences for the factory: First, they cannot export their scrap to countries with better recycling infrastructure - because they can only export finished goods. Indeed, the factory must prove that the variance between the kilos of fabric imported and the kilos of fabric used in exported finished goods has been collected by a waste management company.
Second, although the factory could hypothetically use its scraps to create new finished goods, these could not be sold locally and would need to be exported. The factory has experimented with designing new products made from scraps, but these are niche, more artisanal products that would be extremely expensive to make. The factory doubted that they would be able to find international buyers willing to pay the price.
The supplier also noted that, even if they were able to resolve their legal barriers and could export their scrap to countries with better recycling infrastructure, some of their neighboring countries have bans on importing waste. This prompted someone to suggest that the issue needed to be addressed at a regional level. Could the industry associations engage with regional entities like ASEAN? Could a group of suppliers commission a paper with policy recommendations to help get this issue on the agenda? One supplier commented: “If we really want to do circularity we need different trade policies on waste.” One person suggested that Reverse Resources might be an interesting partner to approach about engaging in the policy space.
Finally, the supplier noted that they had looked into getting their own shredding machine. However, because the country doesn’t have any local spinners or mills, they were unsure of whether there would be a market for their waste. Thus, the financial return on this investment was relatively uncertain. This uncertainty was again compounded by the legal barriers and the fact that this might jeopardize their duty-free import licenses.
The group noted that this supplier’s challenge was not uncommon, particularly for companies operating in Southeast Asia. One supplier based in Pakistan noted that they had a lot more options because of the local spinning infrastructure. This supplier had recently purchased its own shredding machine and was in the process of setting it up.
Other suppliers brought up the Green Machine. Could the supplier rally support from factories producing for H&M to put pressure to introduce the technology in their country? While some participants noted that this could be an interesting avenue to pursue, another doubted whether it was a viable approach - citing the chemical management infrastructure that needs to be in place to support such an option as a barrier.
Someone else suggested reaching out to Re-circled in the US; they are using textile waste to create building materials. Given that the waste management company in question was also active in the construction sector, perhaps this could be a way for them to make money from textile waste beyond incineration?
The supplier sharing their challenge asked the group whether any participants had successfully raised this issue with their buyers. One participant responded that their buyers were, in principle, open to supporting circularity initiatives and that they had more recycling options available in their context. However, they also shared that many of their customers wanted fabrics made with waste coming from their own products (not waste from other brands’ products). Practically, this meant that offcuts from a given brand’s collections would have to come back as yarn made exclusively of waste from said brand’s products. The supplier shared that it was extremely difficult to get their customers to understand how recycling supply chains worked and that it was virtually impossible to trace which waste ended up in which yarn. Achieving this would require a level of immense planning and commitment that most brands were unable or unwilling to give. Moreover, it required immense waste storage requirements that the factory currently did not have.
Several suppliers noted that they’d considered joining the GFA Circular Fashion Partnership as a way to engage with brands and other stakeholders on these challenges but that price had been a big barrier to entry. Participants were unclear about the financial commitment required to join the partnership but joked that they should set up a crowdfunding site to support more suppliers to become part of it.
The conversation closed with a discussion about how poorly the systemic barriers to recycling tend to be understood. Several suppliers noted that this gap could be an interesting opportunity for more formal collaboration – which brings me to the strategic conversations regular Supplier Meet-Up participants have been having. Given the growing number of projects and collaborations somehow affiliated with this group, we are exploring how Supplier Meet-UPs should evolve to reflect this. We’ve also been discussing whether, and under what conditions, the group might want to leverage the Supplier Meet-Up platform to engage with non-suppliers. To this end, the September Supplier Meet-Up is canceled - instead, we will be using the time to make further headway on these strategic questions. If you’re a supplier interested in joining the meet-ups, we’d love to see you at the October Meet-Up.
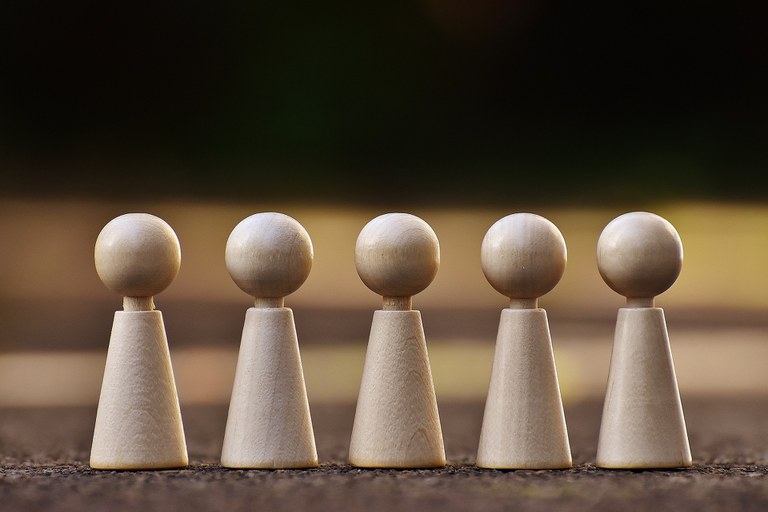
Want to learn more about the Supplier Meet-Ups?
Check out our Supplier Meet-Ups section. Learn more about the latest Apparel Supplier's Guide, the hidden burdens of well-intentioned standards or why manufacturer collaboration could help transform fashion.